How Anti-Foam Control Solutions Enhance Item High Quality and Efficiency
The function of anti-foam control options in commercial procedures can not be overemphasized, as they are pivotal in enhancing both product quality and operational efficiency. By efficiently mitigating foam formation, these services not only guarantee constant product texture across numerous industries yet likewise minimize the risk of contamination, which is essential for preserving high purity standards.
Understanding Foam Formation
Foam development is an usual sensation come across in different commercial processes, usually arising from the communication of liquids with solids or gases. This sensation takes place as a result of the stabilization of gas bubbles within a liquid matrix, leading to the creation of a foamy layer on the surface area. The existence of surfactants, which minimize the surface stress of fluids, can intensify foam formation by facilitating bubble development and stabilization.
Several factors affect foam advancement, including the nature of the fluid, the existence of impurities, temperature, and agitation degrees. High shear pressures during mixing can present much more air right into the fluid, advertising bubble formation. In addition, hydrophobic and hydrophilic substances can connect with liquid surface areas, affecting bubble stability.
Comprehending the mechanisms of foam development is essential for sectors such as food processing, drugs, and petrochemicals, where foam can hinder manufacturing effectiveness and modify product top quality. Identifying the certain conditions that cause foam generation permits much better layout and control of processes, inevitably bring about enhanced functional outcomes. Identifying these essential facets of foam formation establishes the phase for exploring efficient remedies to minimize its negative results in industrial applications.
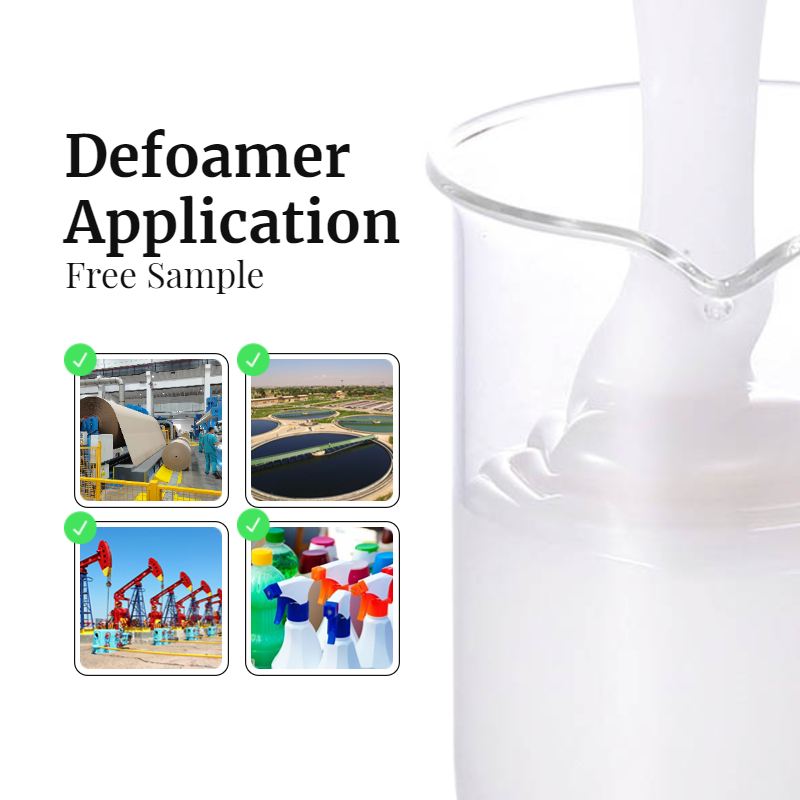
Importance of Anti-Foam Solutions
While foam development can enhance particular processes, its unexpected visibility typically leads to substantial operational difficulties throughout numerous sectors. In production, for example, too much foam can impede the accurate measurement of fluids, leading to inconsistencies in product solution.

The relevance of anti-foam services prolongs past operational effectiveness; they additionally play an essential function in keeping safety requirements. In sectors such as food and beverage handling, where health is paramount, managing foam can stop contamination threats connected with overflow and spillage. Inevitably, the execution of anti-foam services is essential for enhancing manufacturing procedures, guarding equipment, and guaranteeing conformity with sector laws. Their function is vital in advertising total functional quality across diverse sectors.
Benefits to Product Quality
Effective anti-foam solutions significantly enhance item top quality throughout different industries by guaranteeing constant formulation and preventing the intro of contaminations. The visibility of foam during production procedures can bring about irregularity in product qualities, which ultimately influences completion individual's experience. By mitigating foam development, these options help with consistent blending and dispersion of ingredients, causing an item that meets rigorous top quality requirements.
Moreover, anti-foam representatives aid preserve ideal viscosity and appearance, which are vital for products such as coatings, food, and drugs. Anti-Foam Control Solutions. A stable formula is not only visually appealing yet also functionally premium, making sure that products do as intended. In addition, the reduction of foam decreases the danger of contamination, as entraped air can introduce undesirable microorganisms or international particles that endanger product integrity
In applications like fermentation or chemical responses, effective anti-foam remedies support ideal return and product uniformity, which are important for maintaining brand name track record and client complete satisfaction. By prioritizing item quality, makers can cultivate trust and commitment among consumers, inevitably adding to long-term success in the market.
Enhancing Functional Efficiency
A significant decrease in foam can bring about enhanced operational effectiveness in making procedures across various markets. When foam is decreased, it enables smoother operations, consequently lowering downtime connected with foam-related problems. Extreme foam can trigger overflow, interfere with tools functionality, and necessitate regular maintenance interventions, all of which add to inadequacies and raised functional prices.
By implementing efficient anti-foam control services, manufacturers can streamline their procedures, leading to improved throughput and performance. The reduction of foam promotes better blending and reaction times in chemical processes, which is essential in industries such as food production, pharmaceuticals, and wastewater treatment. With a much more steady procedure environment, producers can accomplish extra consistent product outcome, therefore enhancing overall operational dependability.
In addition, boosted operational efficiency can lead to financial savings in resources and power consumption. When foam is controlled successfully, sources are made use of extra properly, resulting redirected here in a reduction in waste and operational costs. Organizations are better placed to fulfill manufacturing targets and react to market needs quickly, eventually contributing to a stronger competitive benefit in the industry.
Picking the Right Anti-Foam Representative
Choosing the proper anti-foam agent is important for sustaining the operational performance obtained with effective foam control. The choice of representative can considerably affect both the performance of the procedure and the high quality of the final product. Factors such as the nature of the foam, the handling atmosphere, and the particular application must be considered to ensure optimum outcomes.
Anti-foam agents can be categorized into 2 main types: silicone-based and non-silicone-based. Silicone representatives are known for their premium performance in high-shear and high-temperature applications, while non-silicone agents might be chosen in industries such as food and beverage as a result of regulative considerations. It is vital to review the compatibility of the anti-foam agent with the products and processes entailed.
Furthermore, the concentration of the anti-foam agent plays a vital function; too much use can bring about unfavorable influences on product top quality, while inadequate quantities may fall short to control foam appropriately. Carrying out thorough testing and pilot this link tests can help determine the most appropriate anti-foam representative for a specific application, inevitably enhancing both product top quality and operational effectiveness.
Verdict
To conclude, anti-foam control options play a critical function in boosting item high quality and functional performance across various markets. Anti-Foam Control Solutions. By decreasing foam formation, these services make sure regular mixing and product structure while minimizing contamination risks. The resultant smoother procedures add to reduced downtime and enhanced throughput, consequently maximizing resource utilization and improving general manufacturing targets. The option of ideal anti-foam representatives better amplifies these benefits, reinforcing their importance in industrial applications.
By effectively mitigating foam development, these remedies not just make sure constant see this page product texture throughout different industries but also minimize the threat of contamination, which is crucial for keeping high pureness standards.Understanding the devices of foam development is critical for sectors such as food processing, pharmaceuticals, and petrochemicals, where foam can prevent manufacturing effectiveness and alter item high quality. The presence of foam throughout production processes can lead to irregularity in product characteristics, which inevitably impacts the end customer's experience. By mitigating foam development, these remedies assist in uniform blending and dispersion of ingredients, resulting in an item that meets rigorous high quality criteria.
Choosing the suitable anti-foam representative is important for maintaining the operational effectiveness gotten through efficient foam control.